FEMTOsecond LASER
The FEMTOsecond LASER μ-machining technology consists of ultra-short pulses that hit the workpiece to vaporize a small amount of material.
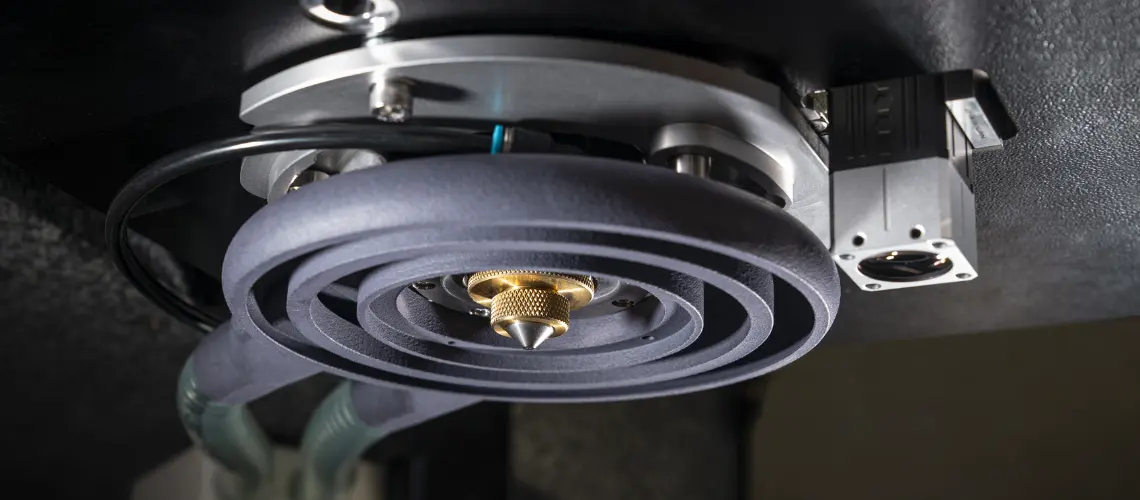
FEMTOsecond LASER μ-machining is the most advanced LASER technology to process a wide range of materials. Thanks to very low heat diffusion time (< 300 fs), thermal effects are avoided. High energy density improves surface and geometries quality, while a high repetition rate ensures excellent productivity.
Function
The FEMTOsecond LASER technology is a perfect match for all industries requiring the highest precision without compromising quality and productivity.
Miniaturized components are used in all kind of devices. Several applications – e.g. in the electronics or MedTech world – are not imaginable without very small and tiny parts. Thus, this requires new ways to produce and manufacture these parts. With FEMTO LASER μ-machining there are various processes possible like drilling, cutting and turning. It's compatible with almost all materials that are otherwise very difficult to machine with conventional tools.
With each FEMTOsecond LASER pulse that hits the work-piece, a small amount of material immediately vaporizes. The material removal occurs in a controlled manner leading to no damage, burrs or any negative influences to the material integrity.
Your benefits:
- FEMTOsecond Laser source < 300 fs
- Highest level of accuracy and productivity
- Stable and repeatable quality
- Cold ablation keeping material integrity (no HAZ)
- Proven performance in 24/7 industrial environment
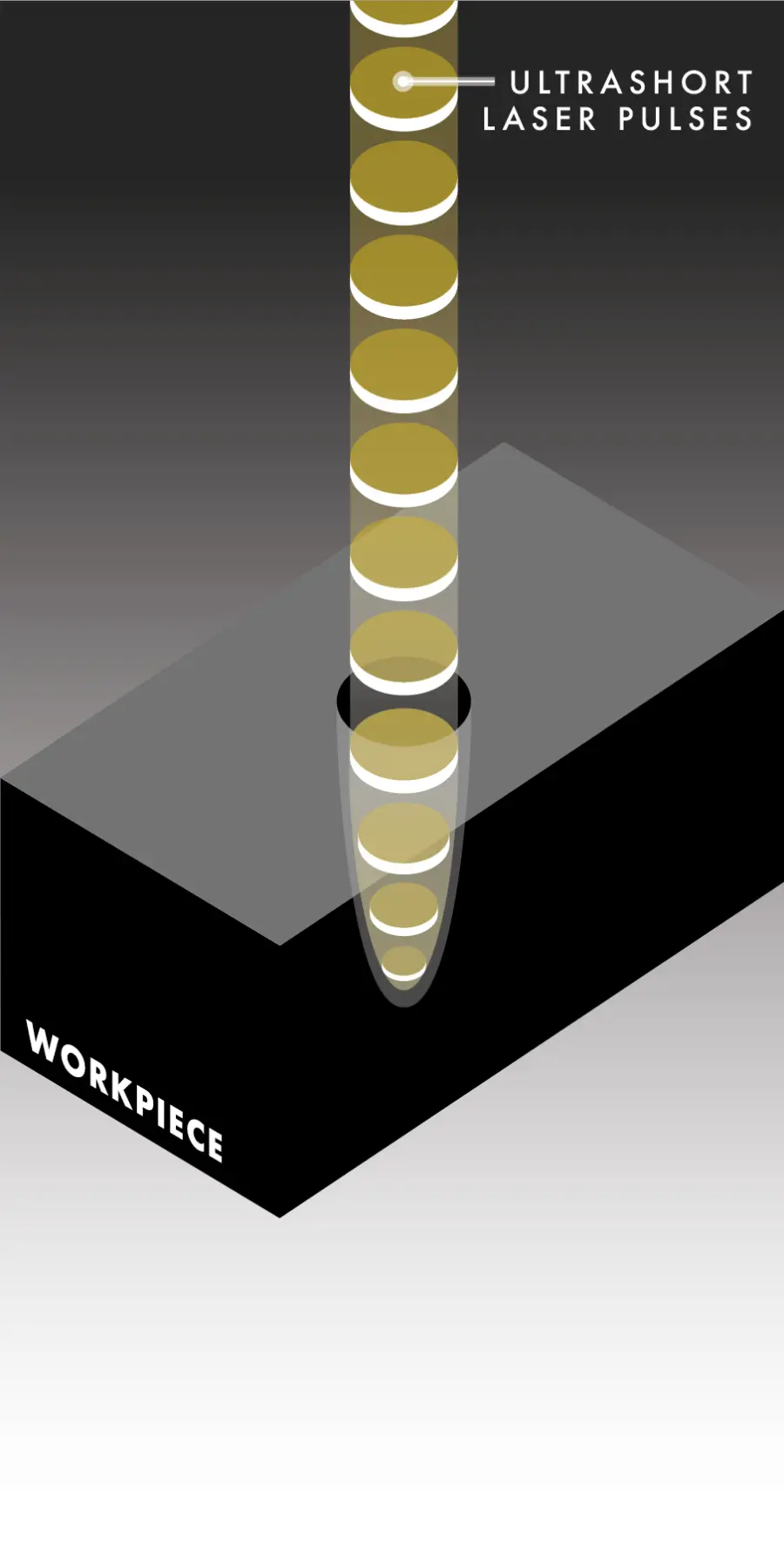
Turning of contacts pins for IC substrates testing industry
Turning of contact pins (wires, bars and tubes) for semiconductors testing industry
Gear cutting operations for the watchmaking industry
What material can be micromachined with FEMTO-second LASER technology ?
Materials family:
Metal alloys
- Aluminium
- Brass
- Bronze
- Non ferrous metals
- Stainless steel
Precious metal
- Copper
- Palladium
- Precious metals
- Titanium
- Tungsten carbide
- Irridium
Bio-metal
- Bio-compatible material
- Nitinol
Engineering plastics
- PEEK
- Polymers
- S1000
- Torlon
- Vespel
- PPS
- Miproplate
Ceramics
- Ceramics
- Hard ceramic
- Photoveel IIs
- Si3N4
- Silicone nitride
- Zirconia
- Silicone carbide
- SiC
Glass
- Glass
Metal
- Hardened metal
- Hardened steel
- Steel
Multi substrates material
- IMS
- Metal baked
- PCB laminates
Gem
- Ruby
- Sapphire
Composite Materials
- Delitt
- FR4
- FR5
What quality and expertise brings Posalux into the FEMTO-second LASER technology?
- Optical and fiber non-destructive measurement to control hole diameter, shape and positioning
- 2D video measuring system with image analysis
- Surface roughness measurement (Confocal Laser 3D)
- Study and trials on demand
What are the micro-machining capabilities of FEMTO-second LASER technology?
- Diameter/ Dimensions down to 20 µm or less
- Size tolerances < ±1.5 µm
- Straightholes (no taper)
- Wallthickness < 8 µm or less
- Corner radius < 3 µm (square holes)
- Orthogonality 89° < … < 91° (square holes)
- Surface quality / Homogeneity of the hole
- No damages, no micro cracks
What means FEMTO?
A FEMTO-LASER is a Laser which emits optical pulses with a duration well below 1 ps, i.e.,in the domain of femtoseconds (1 fs = 10−15 s = Onequadrillionth of one second). It thus also belongs to the category of ULTRAFAST LASERS or ULTRASHORT PULSE LASERS.
What micromachining challenges meets FEMTO-second LASER technology?
- Increased number of holes per guide plate (> 100K) with reduced pitch
- Productivity (square holes 20 x 20 µm < 1.2 sec/hole)
- Repeatability, reproducibility, consistency (several days of production in a row)
- High positioning accuracy (process accuracy within ± 2 µm)
- Stability and reliability (running 24/7)
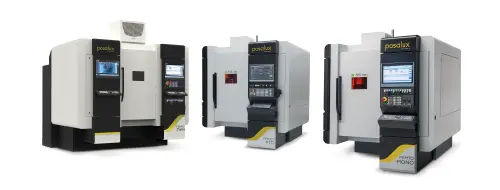
FEMTO
Let’s discuss your
µ-machining operations
If you are looking for a high-tech production system as well as a partner to process state-of-the-art micromachining, you are in the right place.
Discover more technologies
Electrical Discharge Machining - EDM
With the Electro-Erosion μ-machining - EDM technology, material is removed from a workpiece by current discharges between electrode and anode.
Mechanical Micromachining
Mechanical μ-machining technology enables highly detailed shapes and removes material of a workpiece with miniature wearable tools.