Turning of contacts pins for IC substrates testing industry
IC substrate testing poses significant challenges, driven by miniaturization, high-frequency performance, and reliability demands. Addressing cost, time, and variability constraints requires innovative solutions to ensure efficient and effective testing processes.
Contact pins turning application overview
Utilizing techniques such as turning of contacts, pins, wires, bars, and tubes can significantly streamline IC substrate testing. By refining these components to achieve high precision and uniformity, this method enhances test repeatability and accuracy. Additionally, turning these elements allows for faster, more cost-effective testing, catering to the demands of miniaturization and high-frequency performance, thus providing a vital solution to the industry's pressing challenges.
Precision we can achieve when turning contact pins
Harnessing cutting-edge techniques, we're able to accurately turn wire probes made from precious metal alloys. This process enables us to achieve a wire diameter of 41 µm, a probe length of 2.9 mm, and a front tip diameter of just 7 µm. Moreover, the laser processing time to turn both the front and back tips is only 0.4 seconds each, showcasing our process efficiency.
You currently have a vertical probes cutting project and you would like to know more about what we could achieve together?
Give us some more details!
The FEMTOsecond LASER technology is a perfect match for all industries requiring the highest precision without compromising quality and productivity.
Miniaturized components are used in all kind of devices. Several applications – e.g. in the electronics or MedTech world – are not imaginable without very small and tiny parts. Thus, this requires new ways to produce and manufacture these parts. With FEMTO LASER μ-machining there are various processes possible like drilling, cutting and turning. It's compatible with almost all materials that are otherwise very difficult to machine with conventional tools.
With each FEMTOsecond LASER pulse that hits the work-piece, a small amount of material immediately vaporizes. The material removal occurs in a controlled manner leading to no damage, burrs or any negative influences to the material integrity.
Your benefits:
- FEMTOsecond Laser source < 300 fs
- Highest level of accuracy and productivity
- Stable and repeatable quality
- Cold ablation keeping material integrity (no HAZ)
- Proven performance in 24/7 industrial environment
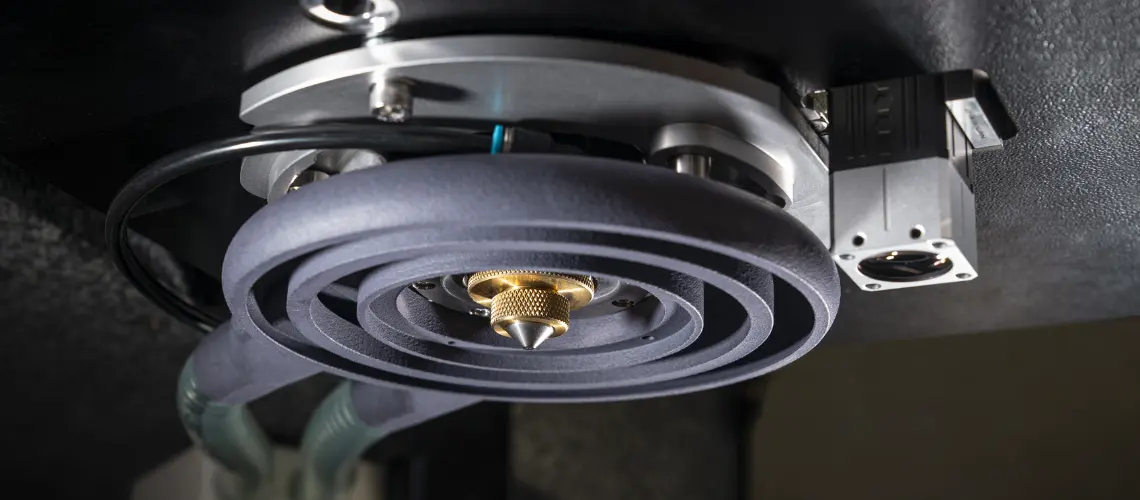
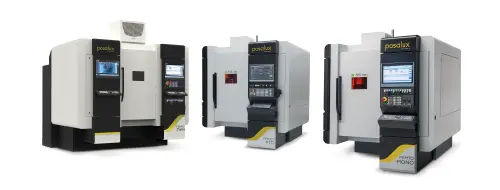
FEMTOsecond LASER machines provide advanced µ-machining solutions for high-tech production. It ensures impeccable surface smoothness and precise machining without thermal residue.
Other applications that might be interesting for you
Turning of contact pins (wires, bars and tubes) for semiconductors testing industry
Drilling and routing of composites and non-ferrous materials for printed circuit boards (PCB) industry
Probe card guide plates micro-drilling for semiconductors wafer testing industry
Let’s discuss your micro-machining operations
If you are looking for a high-tech production system as well as a partner to process state-of-the-art micro-machining, you are in the right place.