Electrical Discharge Machining - EDM
With the Electro-Erosion μ-machining - EDM technology, material is removed from a workpiece by current discharges between electrode and anode.
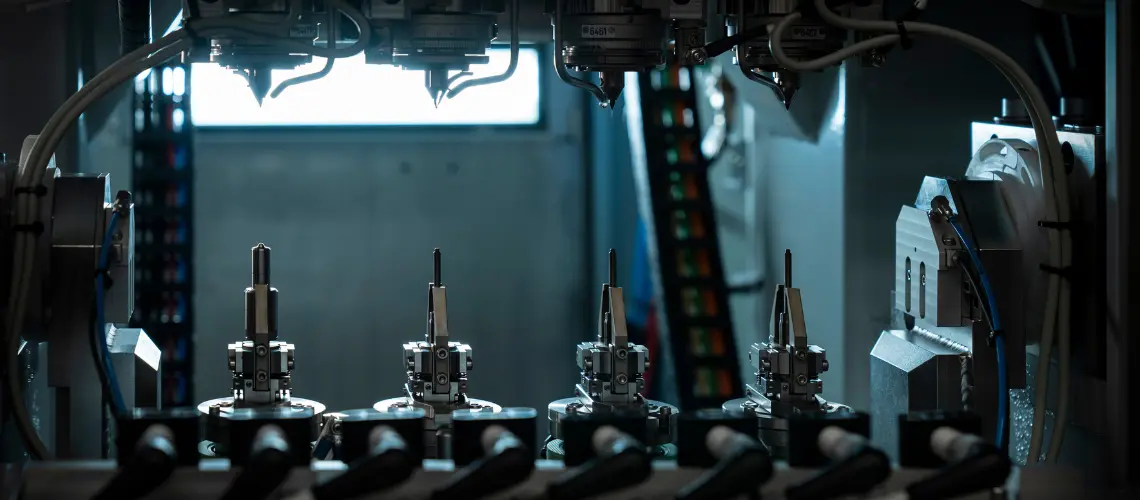
The use of the latest, integrated μ-EDM technology allows machining with high quality and efficiency, meeting the needs of mass production scenarios, especially in the automotive industry.
Function
The process is based on the electro-erosion principle. Material is removed from the workpiece by a series of rapidly recurring current discharges between electrode and anode, separated by a dielectric liquid and subject to an electric voltage. One of the electrodes is called the tool-electrode, or simply the “electrode”, while the other is called the anode, or “workpiece.”
In order to machine high quality micro holes the Posalux EDM machines have a tilting head with deformation by pressure that allows to control the diameter and the shape of the hole, resulting in a run-out of the electrode. The electrode turns on a decentered axis, giving two different gaps, one where sparks erode the material and another, bigger one, allowing a better flushing of eroded materials. In combination with CNC driven axis and a high-speed interface to communicate with the micro EDM generator, perfect micro holes are the result.
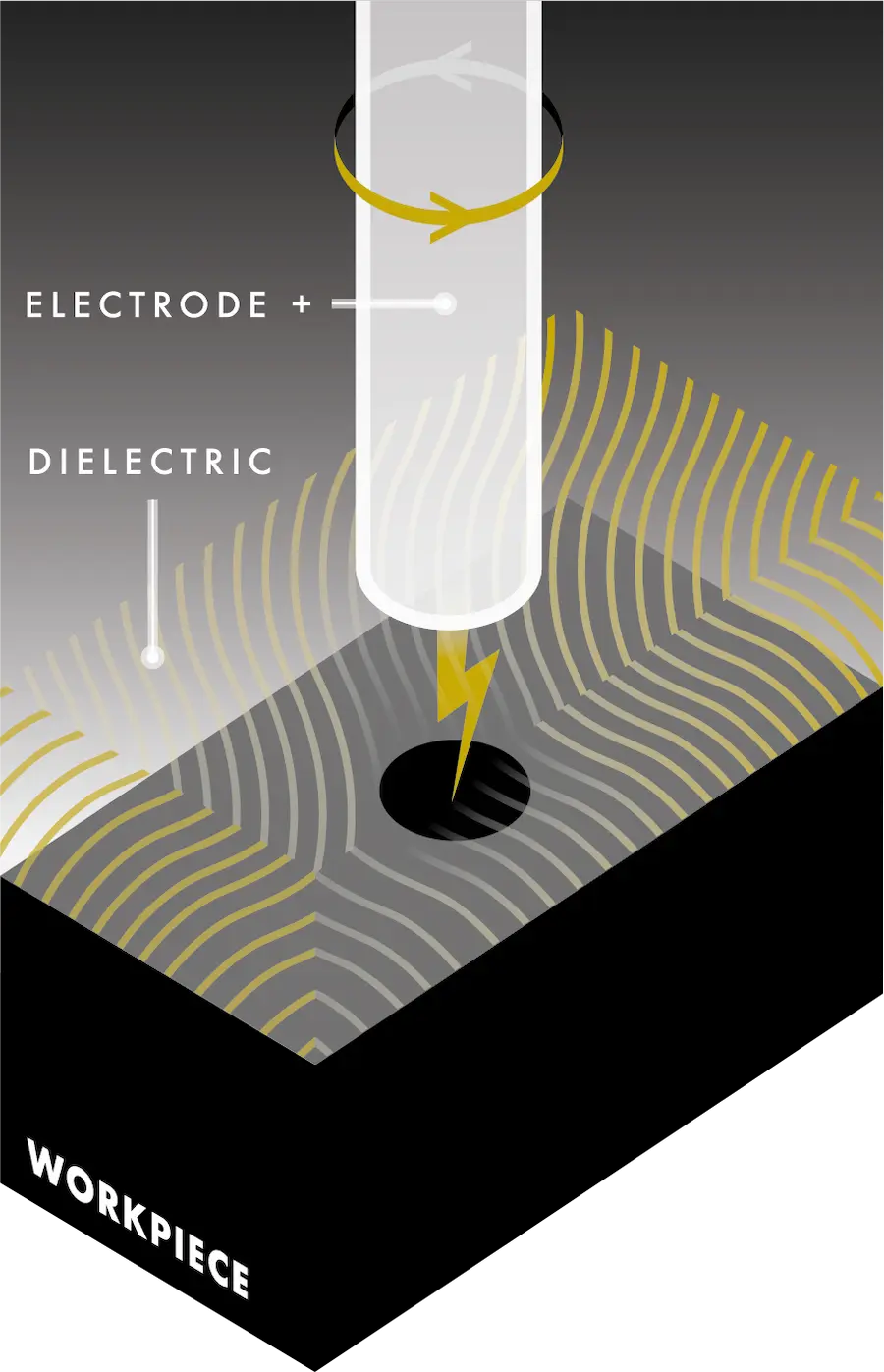
Drilling of GDI shim plate for the automotive industry
Stephole drilling of GDI valve seats for the automotive industry
Spray hole drilling in diesel injection nozzle for the automotive industry
What material can be micro-machined with EDM-Technology?
The EDM Technology integrated in Posalux tools micro-machine parts made of conductive materials.
Materials
- Hardened metal
- Hardened steel
- Steel
Metal alloys
- Aluminium
- Brass
- Bronze
- Non ferrous metals
- Stainless steel
Bio-metal
- Bio-compatible material
- Nitinol
What are the micromachining capabilities of EDM-Technology ?
- Hole diameter from 80 μm in production up to 1.6 mm (0.003 to 0.06 inch)
- Tapered hole with reverse taper up to 150 μm/mm
- Wall thickness / hole diameter ratio up to 12
- All shapes (square, rectangle, oblong, …)
- All conductive material
- Without burr and material deposit, no micro-crack
- Flow stability: +/- 3 % Cp 1.67
- Smooth roughness: Ra < 0.3 μm ; Rz < 1 μm
- 6 holes application diameter 150 μm , thickness 0.8 mm :
Erosion time : 25 s / hole
How is the electrode managed?
- The shifting and guiding collets precisely feed the smallest electrodes available in the market, down to 35 μm.
- The spindle rotation goes up to 3500 rpm for shortest erosion time and optimized material ablation.
- The erosion z-axis with parallel deformation parallelogram type removes mechanical axis resonances.
What specific devices and solutions are included in the EDM Technology?
- Automatic loading / unloading
- Accurate clamping devices
- Software features
- Technical support in defining μ-EDM parameters
- User interface options
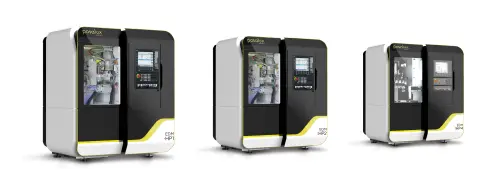
EDM HP
Let’s discuss your
µ-machining operations
If you are looking for a high-tech production system as well as a partner to process state-of-the-art micromachining, you are in the right place.
Discover more technologies
FEMTOsecond LASER
The FEMTOsecond LASER μ-machining technology consists of ultra-short pulses that hit the workpiece to vaporize a small amount of material.
Mechanical Micromachining
Mechanical μ-machining technology enables highly detailed shapes and removes material of a workpiece with miniature wearable tools.