Spray hole drilling in diesel injection nozzle for the automotive industry
The performance and efficiency of diesel engines used in the automotive industry are heavily dependent on the proper functioning of the fuel injection system. Diesel injection nozzles are a critical component of this system, as they are responsible for delivering the precise amount of fuel required for combustion. However, the harsh operating conditions of diesel engines can lead to several challenges which can impact their reliability and performance over time. We are aware that these challenges require a combination of advanced materials, manufacturing processes and maintenance procedures to ensure optimal performance and longevity of the injection nozzles. Let’s tackle these challenges together!
Micro-drilling of diesel nozzles application overview
Micro-drilling of small and precise holes is a critical manufacturing process used to produce injection nozzles for diesel engines.
It requires advanced equipment and techniques to ensure the accuracy and quality of the holes, as even small deviations in size or shape can significantly impact the performance and efficiency of the engine.
Precision we can achieve when drilling spray hole of diesel nozzles
Our priority is to meet your requirements. We can achieve a wide range of spray hole diameters, from 80 μm up to 1.6 mm (0.003 to 0.06 inch), with high precision and accuracy. The process of drilling spray holes is highly efficient, as proven by the erosion time of just 25 seconds per hole for a 6-hole application with a diameter of 150 μm and thickness of 0.8 mm.
You currently have a diesel nozzle spray holes drilling project and you would like to know more about what we could achieve together?
Give us some more details!
The process is based on the electro-erosion principle. Material is removed from the workpiece by a series of rapidly recurring current discharges between electrode and anode, separated by a dielectric liquid and subject to an electric voltage. One of the electrodes is called the tool-electrode, or simply the “electrode”, while the other is called the anode, or “workpiece.”
In order to machine high quality micro holes the Posalux EDM machines have a tilting head with deformation by pressure that allows to control the diameter and the shape of the hole, resulting in a run-out of the electrode. The electrode turns on a decentered axis, giving two different gaps, one where sparks erode the material and another, bigger one, allowing a better flushing of eroded materials. In combination with CNC driven axis and a high-speed interface to communicate with the micro EDM generator, perfect micro holes are the result.
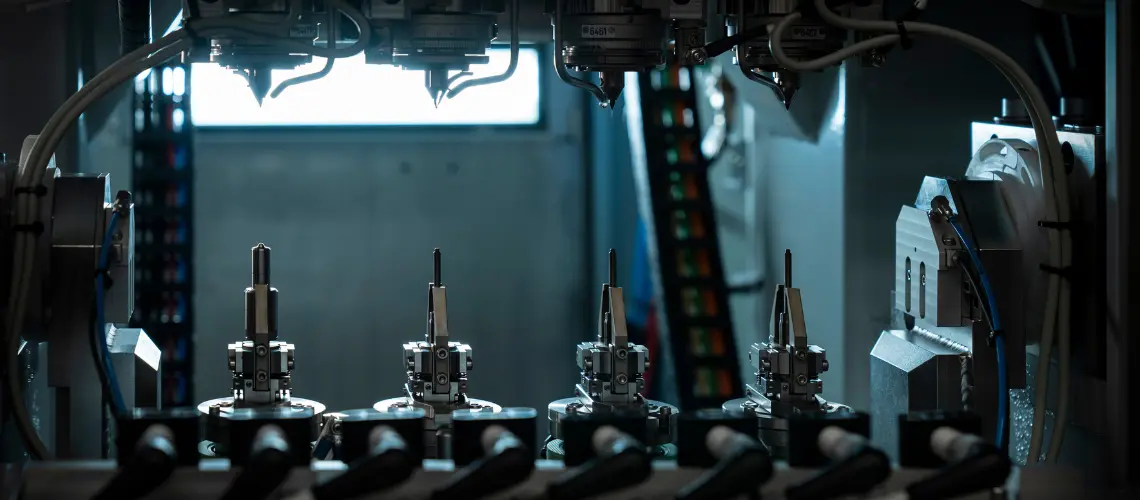
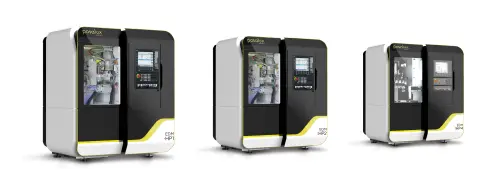
The EDM machine range micromachines parts made of conductive materials with short cycle times and high productivity.
Other applications that might be interesting for you
Drilling of GDI shim plate for the automotive industry
Stephole drilling of GDI valve seats for the automotive industry
Let’s discuss your micro-machining operations
If you are looking for a high-tech production system as well as a partner to process state-of-the-art micro-machining, you are in the right place.