Micro‐drilling with a 5‐Axis Precession Bore System - Practical experience using green and infrared LASERS at Posalux
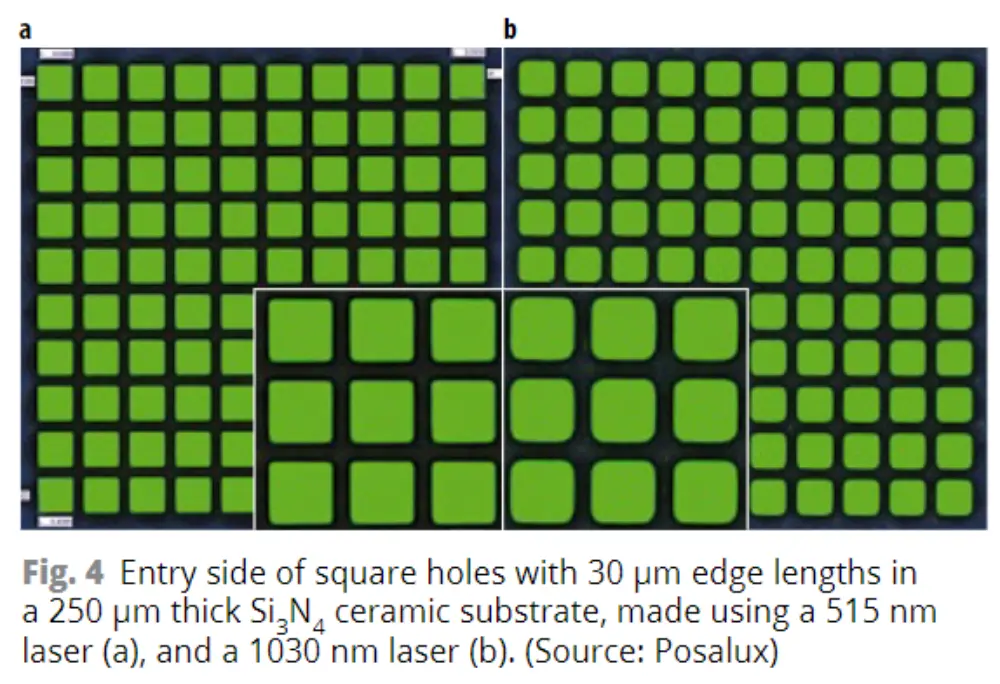
Micro-drilling with a 5-Axis Precession Bore System
Practical experience using green and infrared lasers at Posalux
Relentless miniaturization in both consumer electronics and mechanical en-gineering has brought countless changes to the fabrication of such electronic components as PCBs, control elements, and sensors. This development also affects demands placed on laser processing machines used in micromachining. Difficult-to-handle materials such as polymers and ceramics present a special challenge. The following will describe how machine builder Posalux deals with these growing requirements. Today’s processing limits can be newly defined by employing a precession bore system with a green LASER.
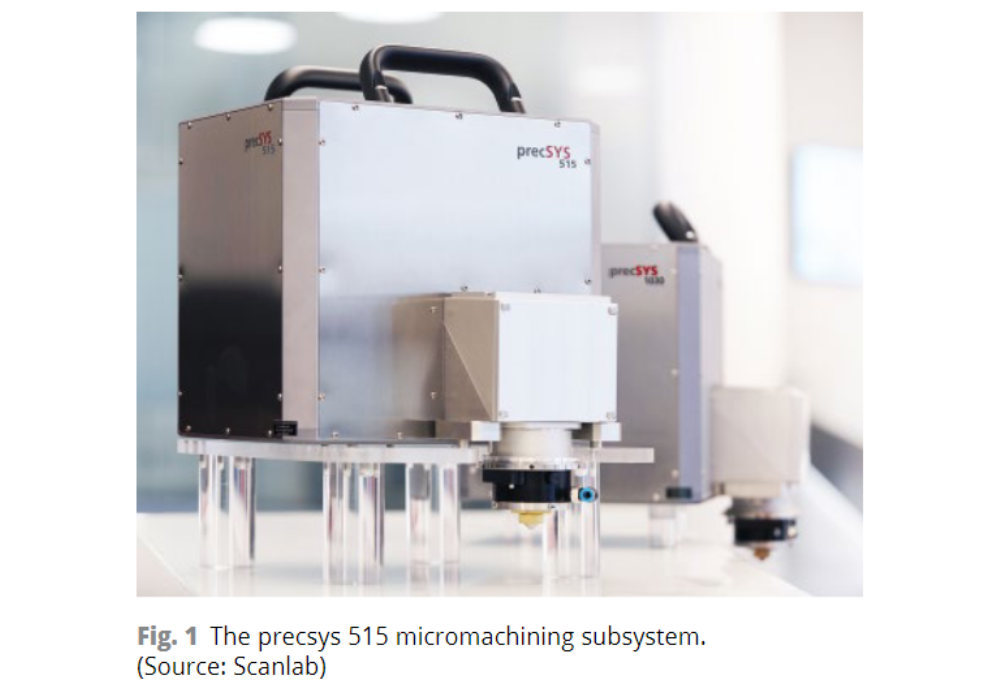
The electronics industry consistently miniaturizes not just its products, but also the devices used to test them. Known as advanced probe cards, these aid in the testing of ICs and assert the most stringent demands on machining. The main component of any probe card is a guide plate consisting of a mechanical substrate with thousands of micro drill holes. Those drill holes must securely and precisely position the probe card’s contact pins to establish accurate contact with the connectors of the semiconductor chip being tested. But mechanical drilling is no longer precise enough for current advanced probe cards. Even worse, variable geometries are needed nowadays. Hence, the benefits of LASER-based machining are obvious: drill hole quality is superior, enhanced bore geometries can be used, and processing times shrunk substantially. Industrial demand for LASER drilling by the micromachining sector has grown noticeably in recent years. Posalux tested the benefits of using a green LASER versus an infrared (IR) system. Particularly interesting under these aspects is the availability of a scan system designed for 515 nm laser beams, which enables the generation of finer lateral structures. Posalux has been supplying high-precision micromachining technologies for high-volume production for several decades. These micromachining tools find use in automotive manufacturing, medical technology, electronics fabrication, and the watchmaking industry.
Quest for ever more precision
To meet the increasing demands of micromachining, Scanlab extended its precsys product family to include a system designed for green LASERS with a wavelength of 515 nm. Compared to IR laser systems at 1030 nm, it is exactly half the applied wave length. This substantially reduces the spot size, thereby enabling much more precise lateral processing of difficult materials. Higher aspect ratios are obtainable at the identical beam divergence. The dispersion of fused silica and the bandwidth of the deployed LASER source play a key role when evaluating the system’s spot size and spot quality. Fig. 2 shows that the change of the refractive index over wavelength at 515 nm is five times higher than at 1030 nm. For 343 nm, this value is a further 3.6 times higher than at 515 nm. In other words, the refractive index of fused silica changes at varying rates across the LASER's bandwidth, thereby introducing chromatic aberration. With classical scan lenses, such color errors can be compensated for by using a glass with a different dispersion. For ultra-short-pulse (USP) LASERS, one such glass that could compensate for chromatic aberration is CaF2. But modern f-theta lenses for USP LASERS typically do not use CaF2 due to limitations in manufacturability and limited temperature stability. So, even with modern f-theta lenses, color errors remain that result from the USP LASER's bandwidth. These color errors depend on the field size, so the largest errors occur at field edges (see elliptical spot on the right in Fig. 3 for 515 nm and 343 nm). This effect also applies to the scan lenses used in the precsys. The effect is particularly strong at 343 nm, so Scanlab decided not to develop a 343 nm drill head.
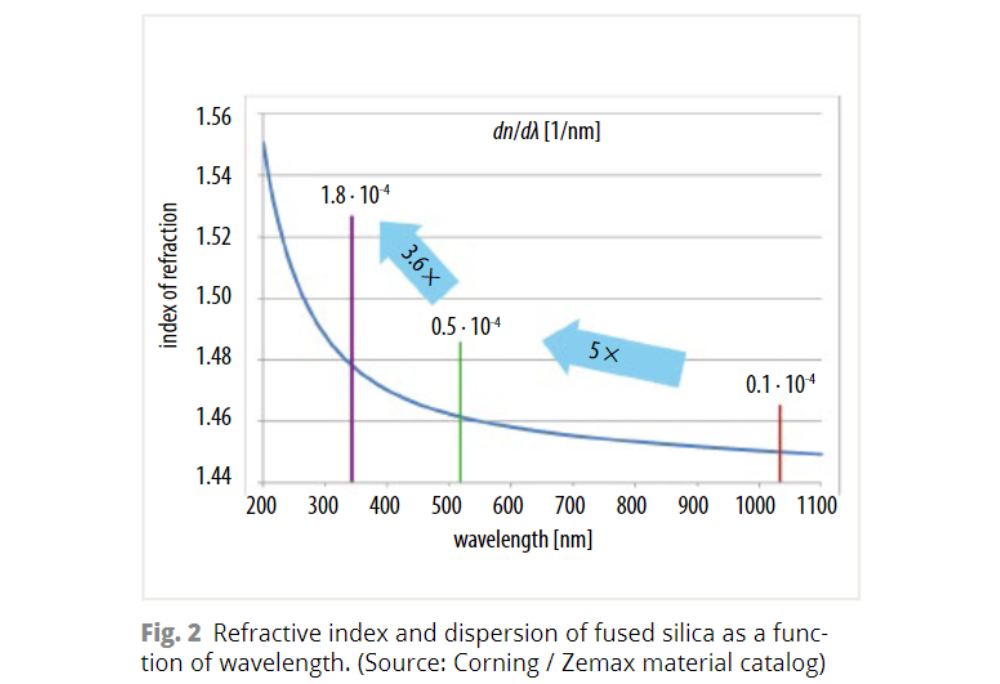
Repeatability as key to success
Posalux integrated the new galvo-based precsys 515 five-axis subsystem into its machine design and subjected it to comprehensive testing. The scan head’s extensive beam-positioning capabilities (in the x, y, z, α, and β directions) provide maximum flexibility for developing new process strategies so that elliptical or linear traversal paths can be defined in 2D or 3D. Meanwhile, all members of the precsys product family now utilize a new approach to servo control that offers even higher rotation frequencies and process speeds during drilling operations. The following documented process examples reflect actual customer requirements and were fabricated by Posalux under real production conditions. Repeatability and precision have the utmost priority here and must be reliably assured throughout everyday production. Fig. 4 shows the entry side of square holes in a Si3N4 ceramic substrate. Holes generated using the 515 nm LASER constantly result in a 3 μm edge radius and these systems fully meet the current stringent needs of customers. In contrast, holes drilled using a 1030 nm LASER only achieved an edge radius of 5 μm. A further application example involved drilling round holes. Fig.5 shows round drill holes with a diameter of 20 μm in a Si3N4 ceramic substrate. The aspect ratio is 12.5:1. Here too, processing was with a green 515 nm LASER. Additional measurements were performed to better evaluate process results. Fig. 6 shows the measured diameters and roundness of 1300 holes drilled using the precsys in a FEMTO LASER machine from Posalux. Readily apparent is that the results remain well below the 2 μm tolerance limit (red lines in graph).The absolute positions of drill holes in the workpiece are depicted in Fig. 7. Again the results remain well below the definded limits, of – in this case – a position tolerance limit of ±3 μm. All these operations and samplings confirm that using a 515 nm laser permits the fabrication of much smaller structures than is achievable with a 1030 nm IR LASER. The diameters, roundness, and positions of drilled holes fulfill the highest precision requirements.
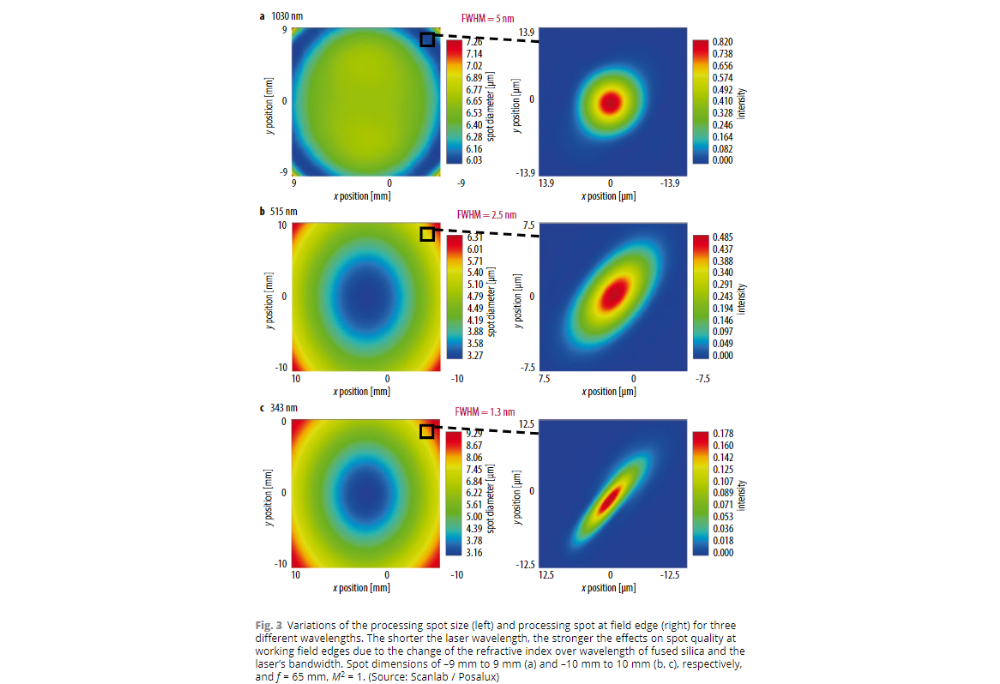
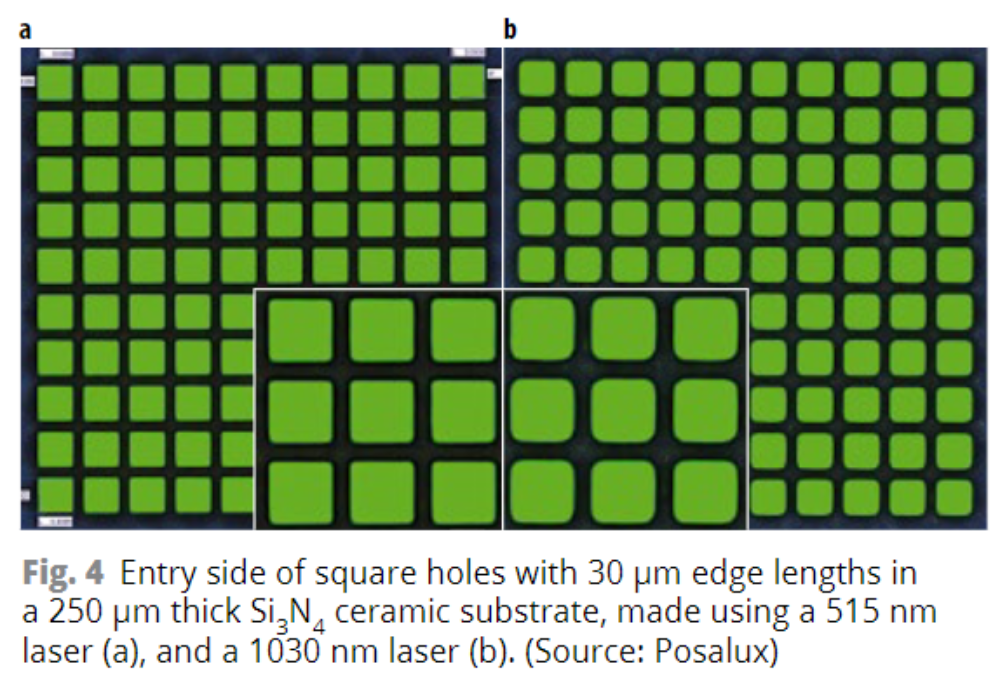
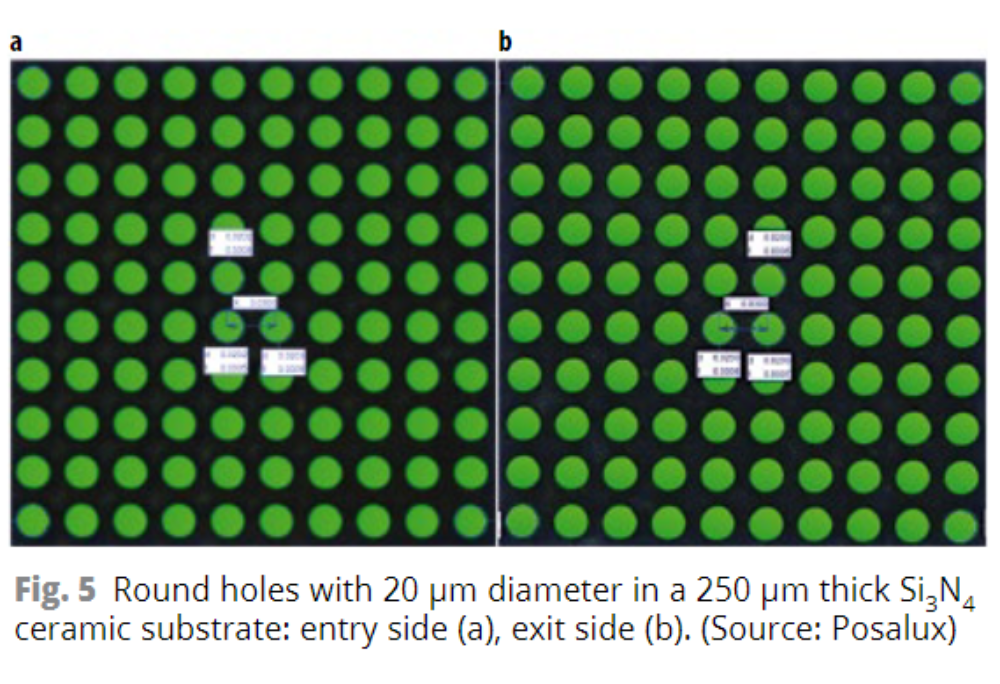
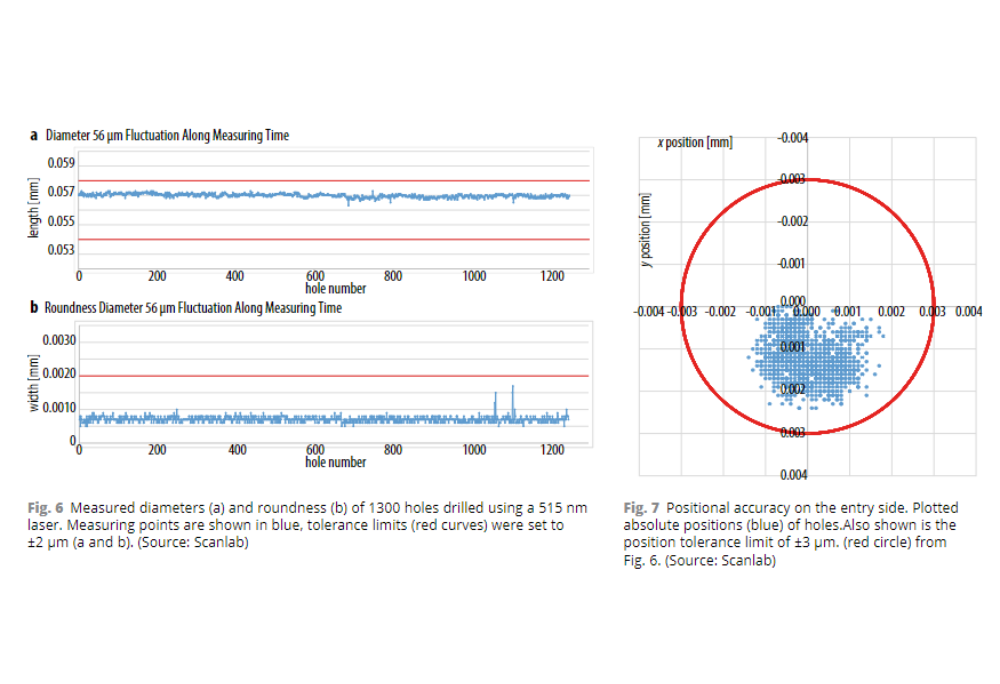
Outlook
Such application examples offer a well-founded insight into the technological advances that will soon also affect other sectors, in addition to the electronics industry. Numerous difficult-to-process materials are coming into focus. These include sapphire, ceramics and glass, as well as the synthetic rubies used, for example, by the watchmaking industry. Further application trials are underway for double valve caps in the automotive sector, as well as in medical technology. The limits in miniaturization and feasibility have yet to be reached.
Full original article PhotonicsViews Volume 17, Issue 3. Micro‐Drilling with a 5‐Axis Precession Bore System (wiley.com)
More news
More learnings
Let’s discuss your micro-machining operations
If you are looking for a high-tech production system as well as a partner to process state-of-the-art micromachining, you are in the right place.